What oil or grease you use is just one element of a lubrication reliability management program. Widening the focus to all aspects of the lubrication process including, storage, handling, dispensing and contamination control is critical to improving reliability. Ensuring you have all the data necessary in making the right maintenance decisions is imperative.
Below is a real-life example of how a Lubrication Audit and Reliability Program can save time and money.
Plant Overview
• The Chicken rendering plant processes approx. 30% of the chicken including: feathers / heads / feet / beaks / offal / blood
• The plant converts these products into high quality fertilizer & stock feed
• Main equipment used includes: cookers / shredders / dryers
• Maintenance is conducted by 2 x fitters
• Mechanical plant includes: gearcases / bearings / fans / pumps /compressors / chains / open gears / electric motors / hydraulics
Lubrication Engineers Observations
• Lubrication Engineers visited when the plant was approx. 12 months old
• Numerous lubricants were in use from multiple suppliers
• Lubrication reliability knowledge of maintenance personnel was low
• Main gear cases located 3mt above the ground with no drain valves fitted
• Manual lubrication of open gears and metal tyres
• No oil analysis program
• No lubricant cleanliness program
• Inadequate breathers fitted
• Not enough hours in the day to conduct required lubrication tasks
• No baseline for lubrication
Internal Audit Results
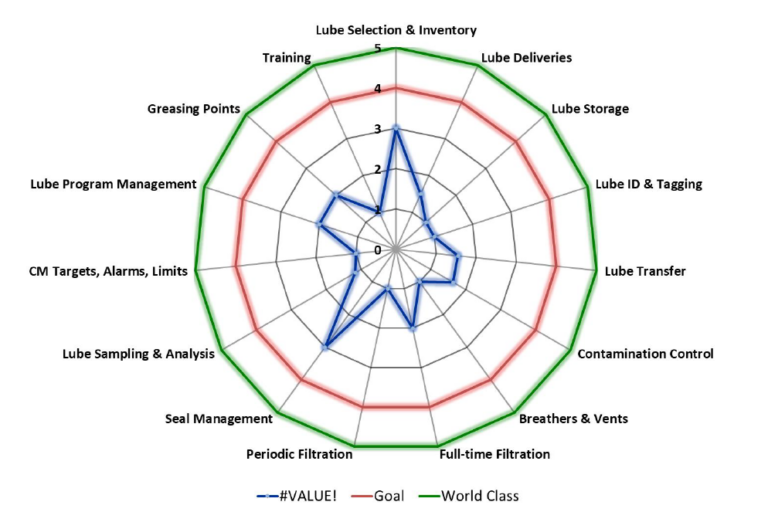
Step 1: Baseline
Step 1 – base line oil samples of all main gearcases and oil filled bearings
Results:
The results of the sample were concerning.
- Gearcases – oil condition ok / high water >600ppm / dirty 24/23/19
- Bearings – PAG oil – high water 8,428ppm / dirty 23/23/21 / silicon
- One of the gearcases had incorrect viscosity oil in service
Gearcase oils being changed on OEM recommendation – 12 months
Bearing oils being changed on OEM recommendation – 3 months

Gearcase Cleanliness
- Air driven 15lpm filter trolley was introduced to improve oil cleanliness
- Majority of gearcases 3mt off ground and had no drain valves fitted
- LE supplied a vacuum transducer which allowed drains to be fitted
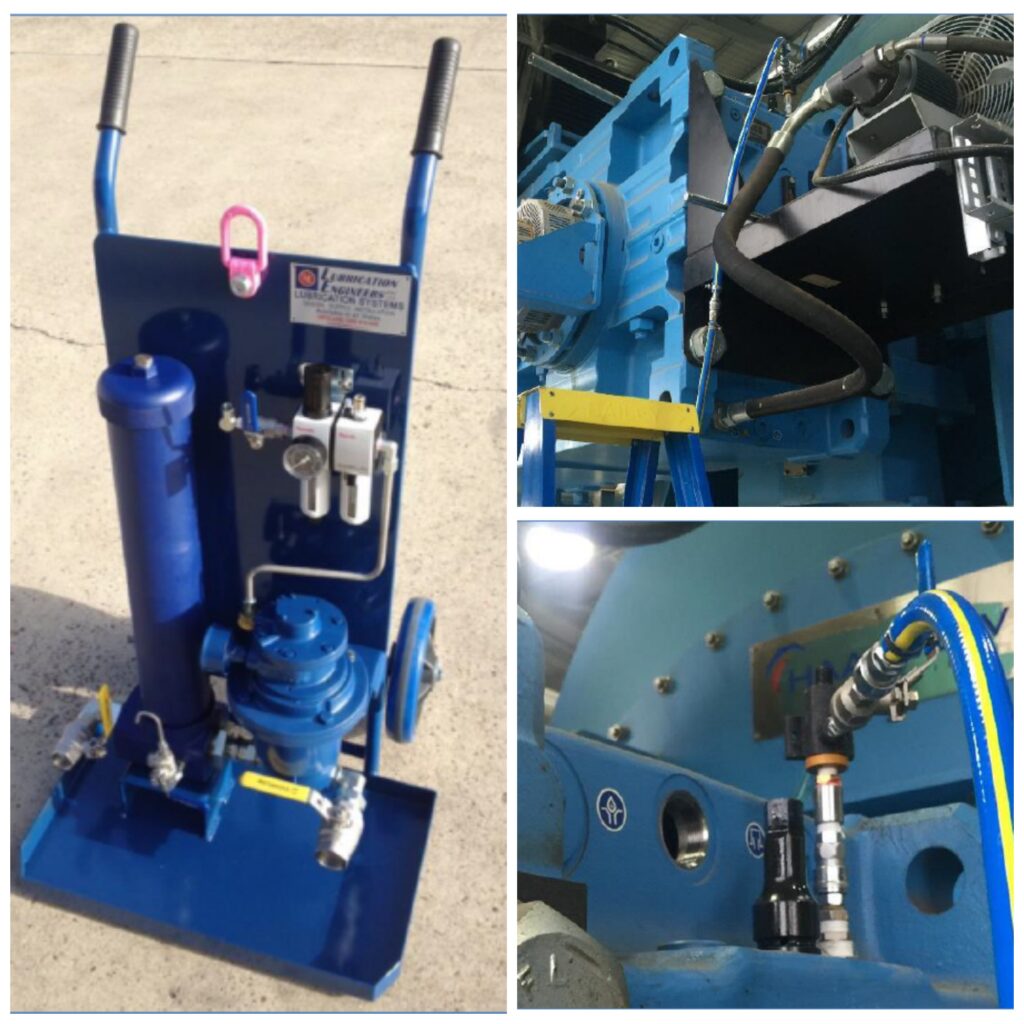
- LE used a filter patch kit to demonstrate effectiveness of the filter cart
- The results can be seen here of the soft offal gearcase after 24 hours of filtering
- All main gearcases were filtered, none required changing – saved 1,550 litres
- Labour savings of approx. 28 hours. Plus no plant downtime.
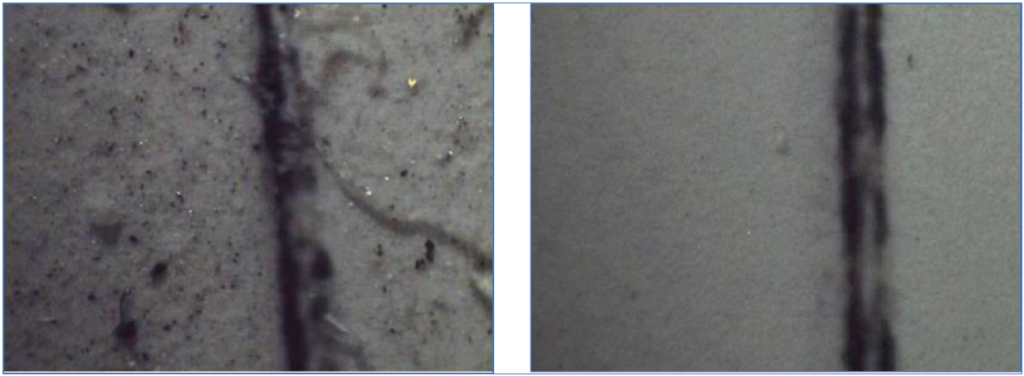
- Gearcases filtered as required based on oil sample results
- Desiccant breathers fitted to all major gearcases and bearings
- Three months after desiccant breathers fitted water ppm reduced from
338ppm to 31ppm (not related to filtering) - Oil cleanliness improved and stable
- 6 monthly oil sampling of gearcases occurring
- Only two gearcases required oil change after 3.5 years
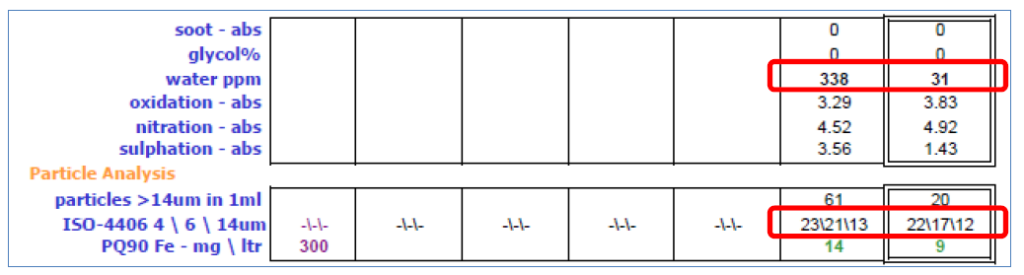
Bearing Lubrication
- Cookers & dryers have large roller bearings with steam fed thru centre
- Equipment OEM filled with ISO680 PAG oil, running intermittently
- Oil analysis showed water content above 9,000ppm & high contamination
- Oil change required at 3 months by OEM, very difficult to drain & refill
- LE recommended the use of Duolec semi synthetic water resistant gear oil
- Extensive cleaning & flushing program
- Fitted desiccant breathers
- Fitted clear sight glasses on drains to see any water
- Visually inspected bearing elements after 12 months
- Water <100ppm / Silicon levels still high
- 1 lpm custom kidney loop currently being built
- Estimate 4 year drain instead of 3 months

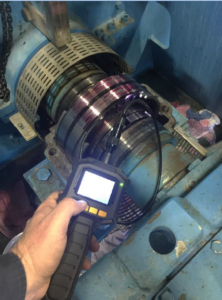
Crusher Open Gears
- Air driven 15lpm filter trolley was introduced to improve oil cleanliness
- Majority of gearcases 3mt off ground and had no drain valves fitted
- LE supplied a vacuum transducer which allowed drains to be fitted
- Single point lubricator fitted, two outlet drips onto gears
- Translucent open gear lubricant introduced, gear condition monitored
- Monthly replacement of lubricant pouch
- Fitted similar systems to Blood dryer and Tri-Canters
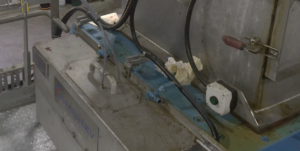
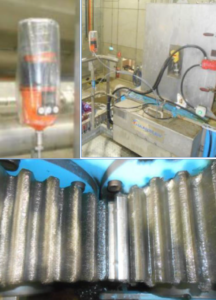
Grease Rationalisation
- Previously approx. 7 x greases in use, now only 4x.
- LE1275 – Main plant grease (Aluminium complex)
- LE1282 – Electric motor grease (Polyurea)
- LE3752 – High impact / load & wet applications (Lithium complex)
- LE5180 – Open gear applications (Bentone)
Summary
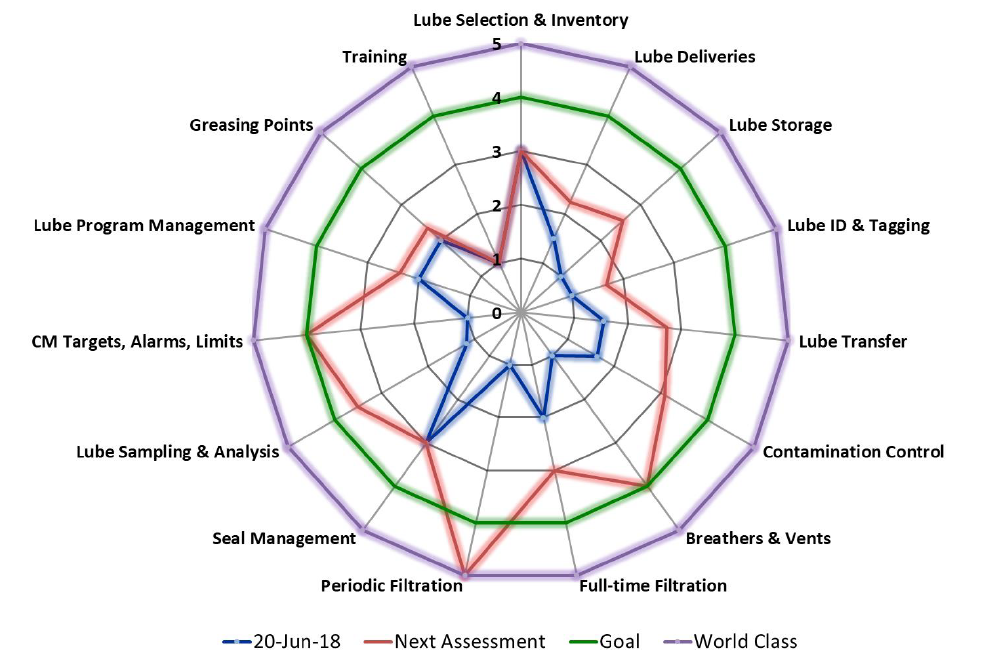
- Lubrication tasks at this site are now at manageable levels
- Key equipment is monitored on a regular basis
- Oils are only changed as required rather than at OEM intervals
- Greases have been rationalized
- Automatic lubricators used where access or intervals require regular lubrication to occur
- Oil changes saved >4,500 litres
- Less waste generated
- Technical support for all lubrication related issues supplied by LE